Oct 18, 2023
How cutting-edge technology is revolutionizing jewelry manufacturing
Jewelry has always been an important part of our history and culture. What has changed is the way we make it.
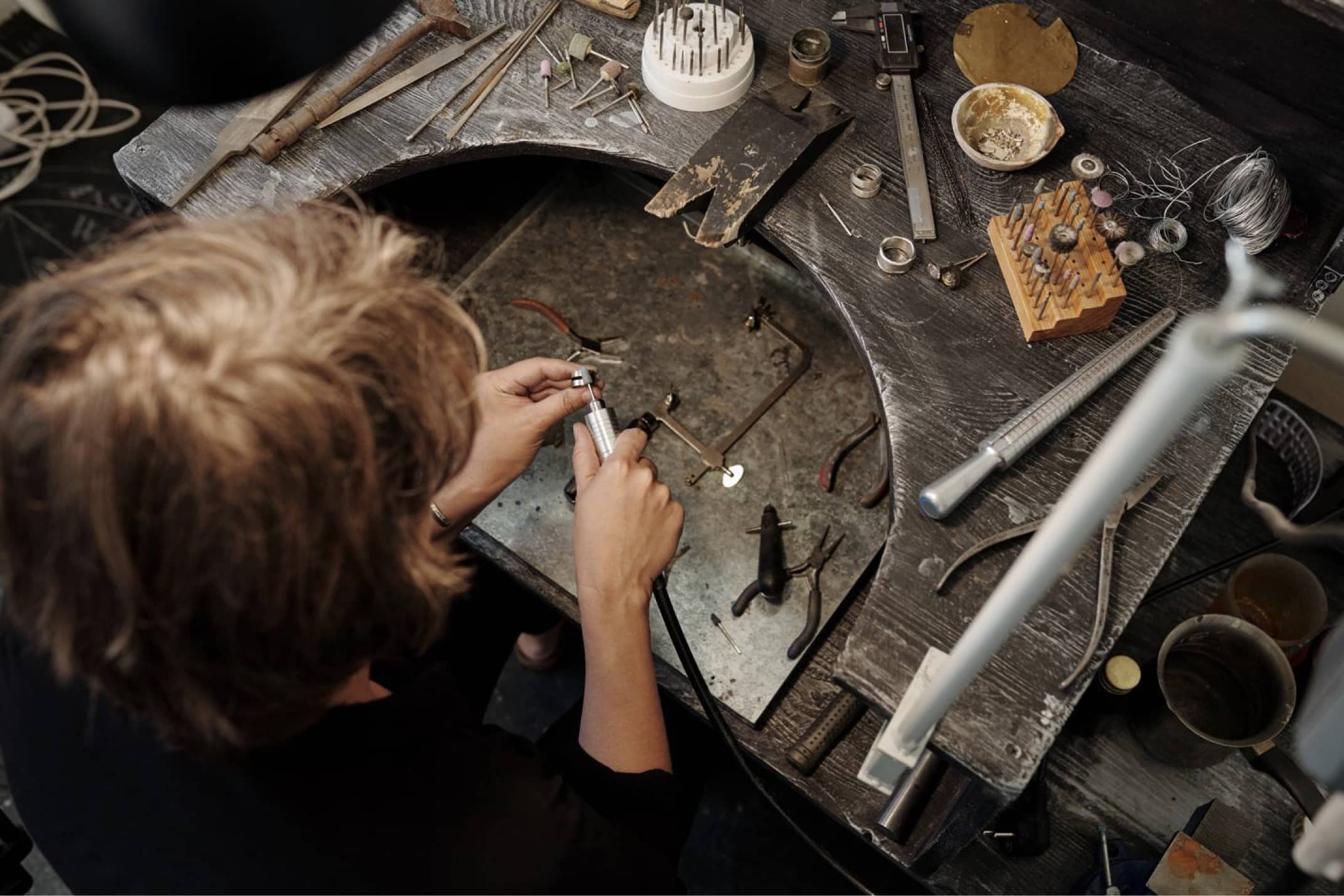
Jewelry has always been an important part of our history and culture. What has changed is the way we make it. People moved from using smaller tools via traditional methods to manufacturing jewelry pieces in labs. Today, the landscape of the jewelry industry has evolved even further with manufacturers using technology to reimagine the craft.
In this blog, we dive deep into how technology has impacted the jewelry manufacturing process to streamline processes and enhance creativity. Let’s get started, shall we?
Table of Contents:
- It’s all in 3D
- Dreaming in precision
- Creating is the new reality
- Automation in process
- Sustainability is key
- Conclusion
It’s all in 3D
Yes, 3D printing for jewelry manufacturing has been in use for a few years now, but it has only recently become affordable. This easier access has helped jewelers in the US to work on intricate designs at a higher speed and larger volumes. 3D printing also helps in layering materials like wax, which can build prototypes with incredible accuracy. So, manufacturers get a realistic view of the product before releasing it into the market. People are building houses with 3D printing, so designing jewelry pieces is only fair.
Dreaming in precision
Jewelers use computer-aided design (CAD), a software that allows them to bring their artistic visions to life with utmost precision. It helps them exact outputs, so that they can iterate and experiment before sending a design into production. Manufacturers use computer-aided manufacturing (CAM) to transform the CAD designs into tangible jewelry pieces. This helps eliminate human errors as well as the numerous traditional steps to manufacture jewelry at lower costs.
Creating is the new reality
We’ve heard of this technology being used to alter matter at molecular and atomic levels. So, why not use it to manufacture new gemstones and diamonds with unique properties? Nanotechnology is enabling jewelers to create pieces that are incomparably more brilliant and flawless than the gems that were formed naturally. How cool is that?
Automation in process
If you go back about two decades or so, jewelers were hesitant to use CAD. However today, most of the industry has switched to using a CAD model. That’s where automation in jewelry manufacturing is right now. Some jewelers are adopting it while the others will get to it 20 years down the line. But it’s here and it’s happening, and for good reason. It streamlines processes, minimizes human error, and enhances the quality of the product.
Sustainability is key
Today, the world has become more conscious about reducing the impact on the environment. And jewelry manufacturers in the US are not far behind. They make sure to precisely allocate material with barely any room for errors. That helps with minimizing waste and increasing sustainability of the manufacturing process.
Conclusion: The future is already here
The adoption of technology in jewelry manufacturing is far from over. In fact, it is still evolving further with the use of artificial intelligence (AI) and machine learning (ML). These help with predictive analytics and design recommendations – all based on customer data and preferences. The use of technology is enhancing efficiency and streamlining the jewelry manufacturing process, so it’s not surprising that jewelers are embracing it. It’s time we bridge the gap between the traditional ways and technology. What say?
If you’re looking for something to help you with streamlining your manufacturing operations and maximizing profitability, try the Luxare Enterprise Resource Planning (ERP) software. Check it out here.
Sustainability is key
Today, the world has become more conscious about reducing the impact on the environment. And jewelry manufacturers in the US are not far behind. They make sure to precisely allocate material with barely any room for errors. That helps with minimizing waste and increasing sustainability of the manufacturing process.
Related Resources
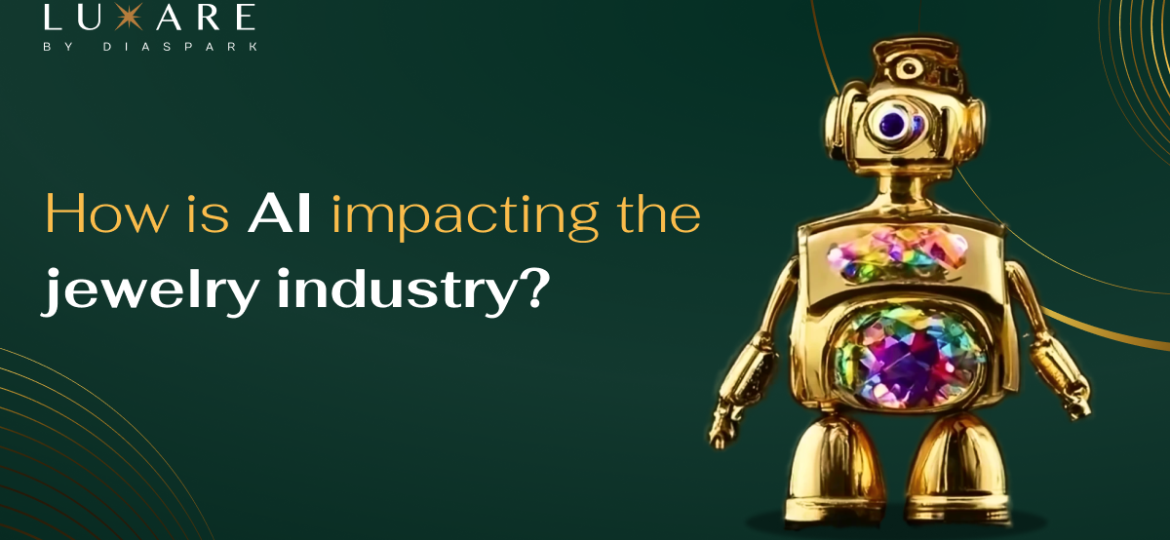
The Sparkling Future: How Artificial Intelligence is Revolutionizing the Jewelry Industry
Artificial intelligence has entered the jewelry industry chat.
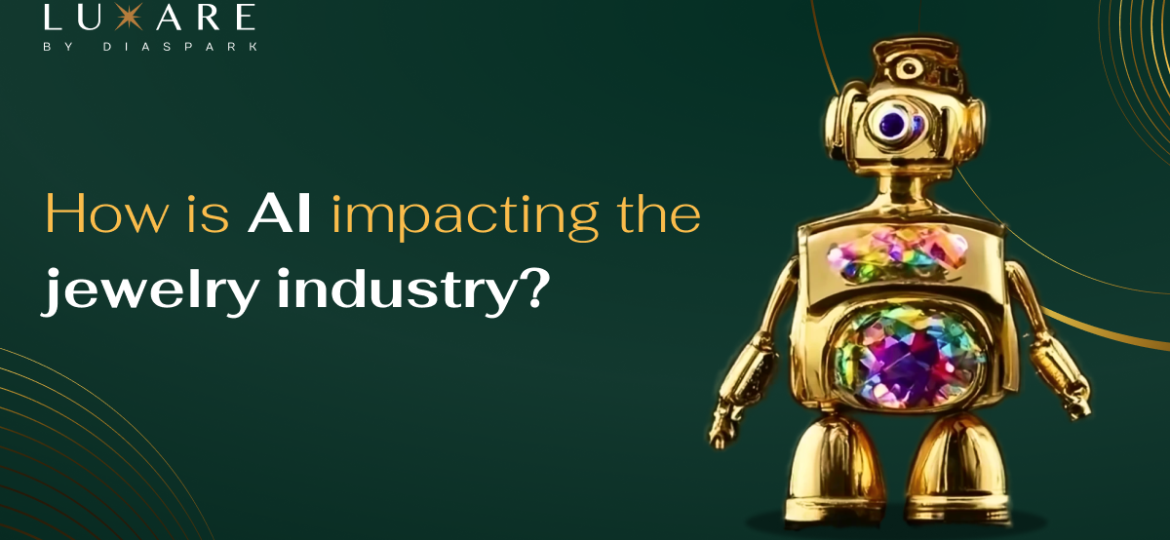
The Sparkling Future: How Artificial Intelligence is Revolutionizing the Jewelry Industry
Artificial intelligence has entered the jewelry industry chat.
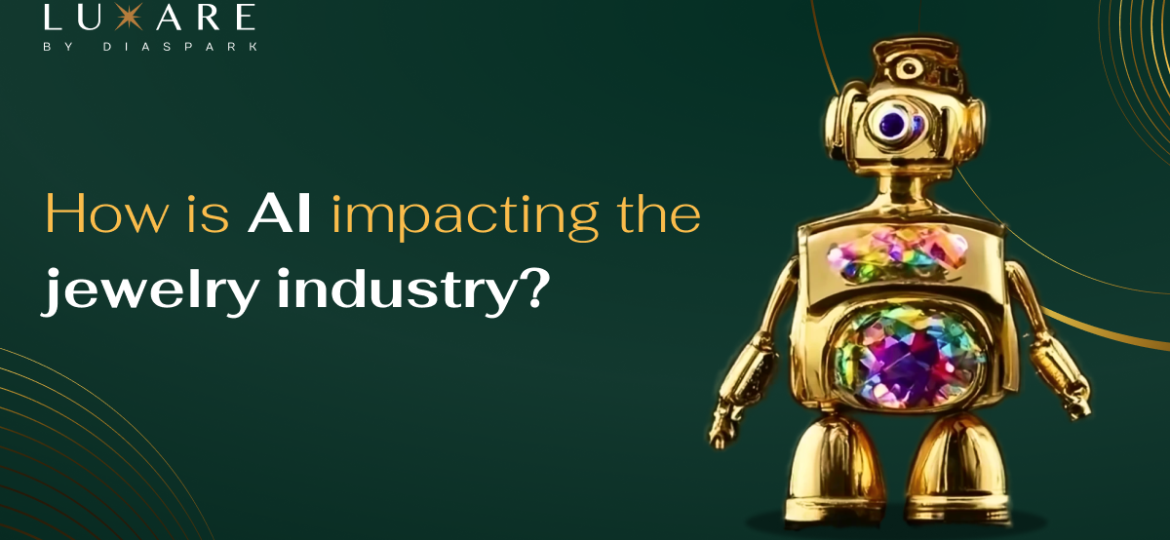
The Sparkling Future: How Artificial Intelligence is Revolutionizing the Jewelry Industry
Artificial intelligence has entered the jewelry industry chat.
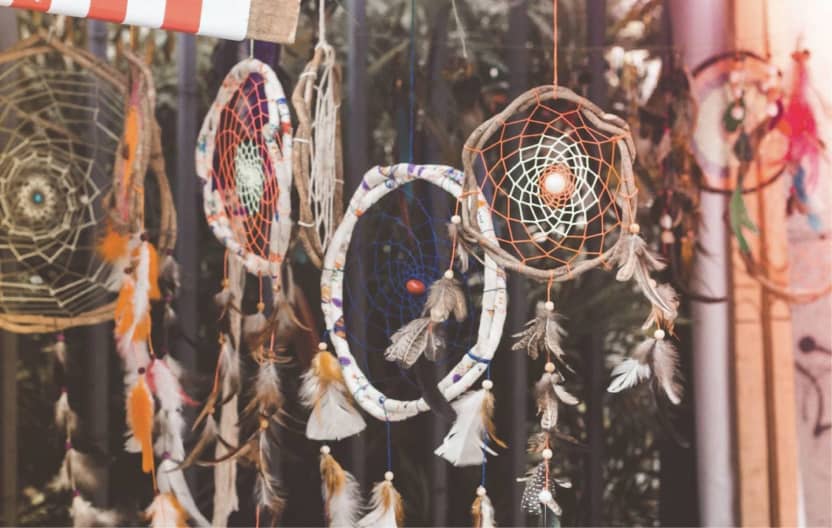
Native American jewelry: A memoir
Renowned for its distinctive style and designs, Native American jewelry has been in the making since the earliest times of the Aztecs, Maya, Inca, and Anasazi.
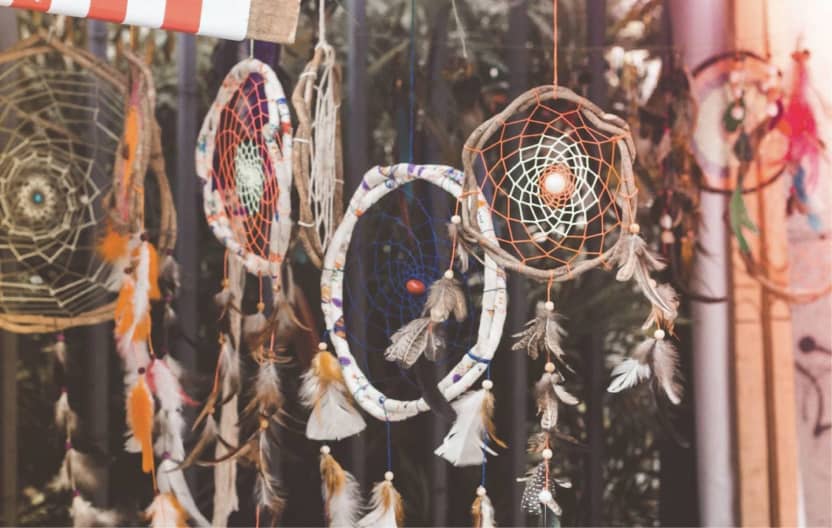
Native American jewelry: A memoir
Renowned for its distinctive style and designs, Native American jewelry has been in the making since the earliest times of the Aztecs, Maya, Inca, and Anasazi.
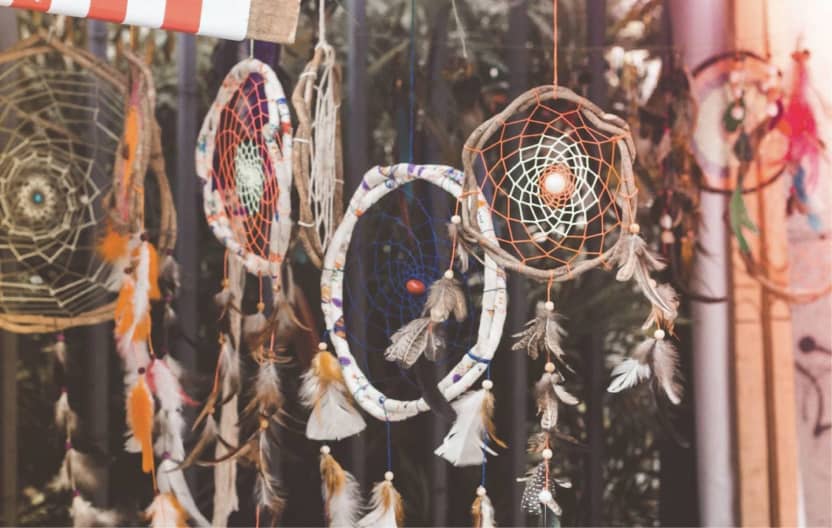
Native American jewelry: A memoir
Renowned for its distinctive style and designs, Native American jewelry has been in the making since the earliest times of the Aztecs, Maya, Inca, and Anasazi.
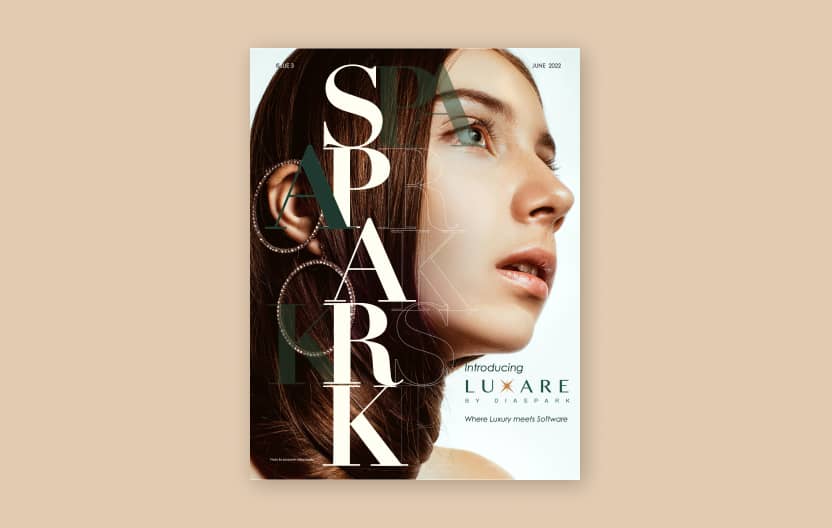
Spark magazine, Issue 3: Introducing Luxare
In this issue, we launch our Luxare brand, an organization built with the vision to deliver cutting edge software products to transform businesses in the luxury space.
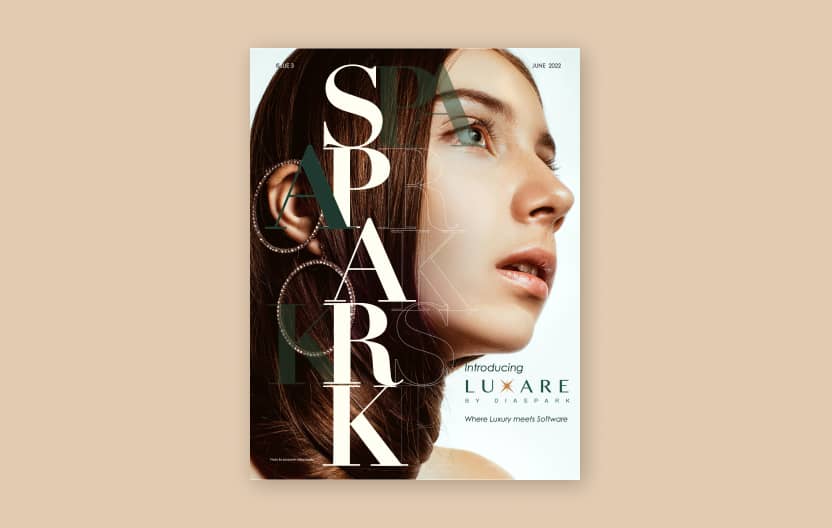
Spark magazine, Issue 3: Introducing Luxare
In this issue, we launch our Luxare brand, an organization built with the vision to deliver cutting edge software products to transform businesses in the luxury space.
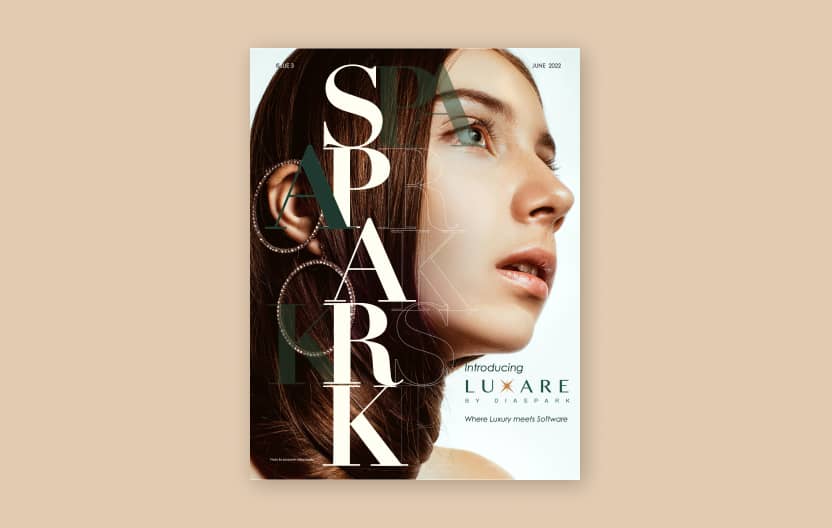
Spark magazine, Issue 3: Introducing Luxare
In this issue, we launch our Luxare brand, an organization built with the vision to deliver cutting edge software products to transform businesses in the luxury space.